In the production of the paper industry, it is of special significance for the sustainable development of enterprises to realize industrial upgrading by using automation and intelligent technology. Energy saving and consumption reduction and production efficiency improvement are the only way for the development of enterprises, so the production equipment is gradually realized by automation and intelligence. In 2018, our company newly installed a complete set of automatic stackers on the No.18 machine, in which the key equipment is the intelligent manipulator for handling the tray grabbing part. Its purpose is to promote the deep integration of industrial informatization and industrial intelligence, and reduce the waste of finished packages brought by manual packaging, and greatly reduce the labor cost. This paper introduces the startup and operation of the intelligent manipulator, the manual and automatic state and the common troubleshooting methods.
The intelligent manipulator starts automatically for the first time
The manipulator is responsible for grabbing the finished paper tray from the slitter. If all the finished paper trays on the trolley are qualified products, the manipulator will run automatically. If the finished paper trays on the trolley are defective and need to be rejected, the automatic mode will be changed to manual mode, and the operator will reject the individual paper trays, and then the manual mode will be changed to automatic mode.
Ready to start
Make sure that the intelligent manipulator is at or near the initial position, and that there is no workpiece on the inflation shaft, as shown in Figure 1. If the intelligent robot is powered on, it is far from the initial position or there is a paper tray on the inflation shaft, it is necessary to manually run to the initial position and put down the paper tray.
Confirm data
Select the option "Stacking Station" on the "System Status" page of the touch screen, where the setting of "Stacking Diameter" should be greater than the diameter of the batch of paper trays and less than half the side length of the current bottom shot; Confirm that the value in the current stacking position is the same as the number of the current stacking tray. If not, manual intervention is needed to set the stacking.
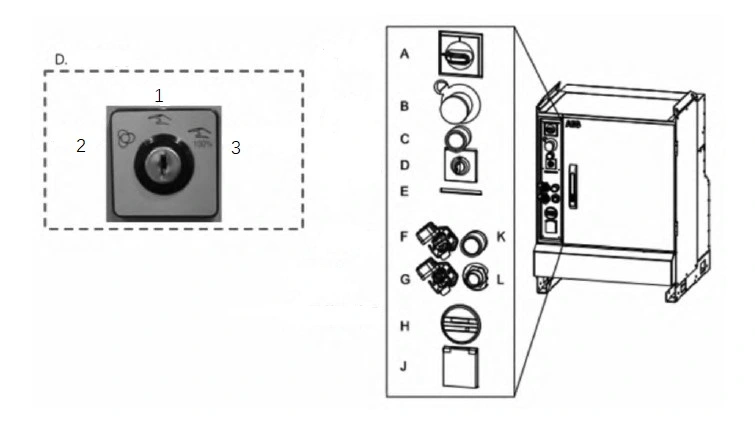
Master switch a b emergency stop c motor power-on d mode switch F.USB port g network cable l teaching device port 1. Manual deceleration mode 2. Automatic mode 3. Manual full-speed mode.
Figure 1 Intelligent manipulator control panel
Automatic running position
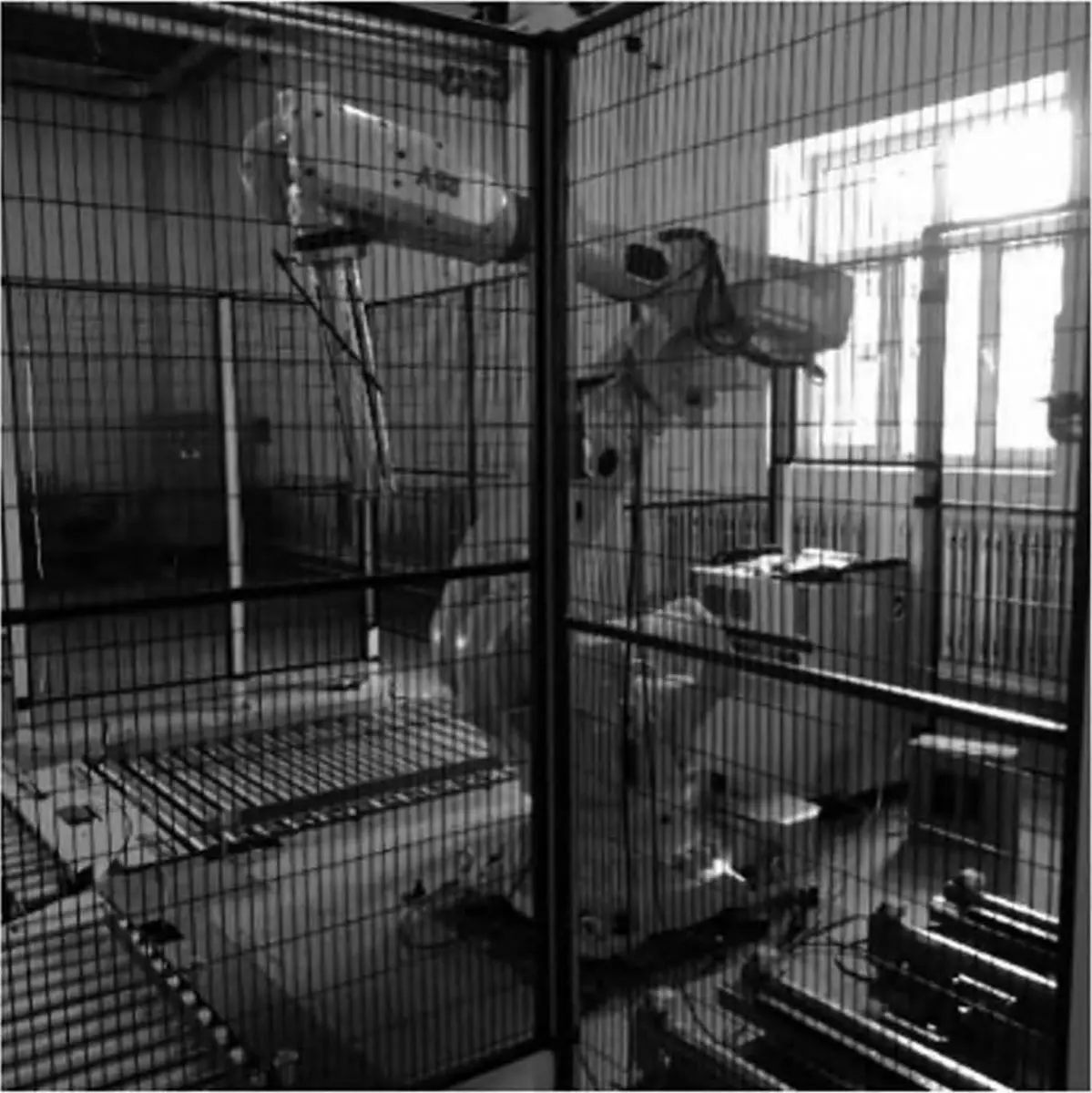
Figure 2 Automatic position of the intelligent manipulator
Turn the key knob of the intelligent mechanical flashlight cabinet to the left automatic mode, and click "OK" on the screen of the teaching device. The icon on the screen turns green, indicating that the automatic mode has been turned on. The automatic position of the intelligent manipulator is shown in Figure 2.
Run ready
On the system status page, click "Run Preparation", wait until "Run Preparation" turns green, click "Program Reset", and finally click "Start Running". When "Run Preparation" and "Start Running" are both green, the intelligent manipulator can start running. The manipulator needs to grab the finished paper tray on the trolley. If it is found that the trolley is in place and the intelligent manipulator is still not running, click "Hand Grip Off" on the touch screen, and then click "Start Running", and the manipulator will automatically run.
Operation status change
Intelligent manipulator emergency stop
In case of emergency, you need to press the emergency stop button. The buttons that can control the emergency stop of the intelligent manipulator include the emergency stop button of the console, the emergency stop button of the intelligent manipulator teaching device, the emergency stop button of the manual disk picking station, the emergency stop button of the trolley electric cabinet, the emergency stop button of the intelligent mechanical flashlight cabinet and the emergency stop button of the safety door near the intelligent manipulator. After the danger is removed, the corresponding reset operation can be carried out.
Running pause
During operation, if you need to suspend the intelligent manipulator, press the following operation: when the intelligent manipulator is in a safe position (at a distance from other equipment), click the "Stop Running" button in the system status page (Figure 3). When the "Ready to Run" and "Start Running" buttons turn gray and the "Stop Running" button turns red, it means that the intelligent manipulator has been suspended.
Run on
If you need to continue running after the pause, click the "Run Preparation" button, and then click "Start Running" when the "Start Running" turns green and the "Stop Running" turns gray, the intelligent manipulator can continue running.
Change the running speed
The speed of the first operation mode of the intelligent manipulator is 10%. If you want to change the speed, click the blue and white progress bar in the system status page (Figure 3), select the corresponding speed, and then click the "Change Speed" button. This operation should be carried out during the operation of the intelligent manipulator.
Manual operation
Run to the initial position
If the intelligent mechanical hand is not in the initial position when it is powered on, it needs to be manually moved to the vicinity of the initial position: turn the intelligent mechanical flashlight cabinet key to the middle position in manual mode; Click the G key to switch the operation mode. Click continuously, and you will find that the lower right corner of the screen is 1/3 and 4/6 switched to each other. Take the 1/3 as an example. When the enable key on the back of the teaching device is pressed, twisting the rocker left and right moves on one axis. Twist the rocker up and down for 2-axis motion; Twist the rocker counterclockwise for 3-axis motion. The rocker is an analog rocker, which is slow when lightly twisted, fast when heavily twisted, and lightly twisted when the direction is not confirmed.
Manually operated air expansion shaft
When the intelligent manipulator is in the manual state, click the A key to switch the state of the pneumatic shaft. If the air inflation shaft does not move, check whether the electric cabinet of the dish picking trolley is powered on and whether the air source pressure is normal.
Parameter setting
On the console screen, the status page of the intelligent manipulator provides parameter settings that may be used when the intelligent manipulator is running, including palletizing settings, trolley pick-up compensation, and palletizing position settings.
When entering the parameter setting, the user needs to log in to the account, where the palletizing type represents that the current palletizing is 2× 2 or 2× 1; The number of stacking layers represents the number of layers that need to be stacked, and this data has been automatically calculated by MES system. If it is correct, it does not need to be changed; Bottom beat height, because different bottom beat heights are different, it needs to be manually measured and written; Two stacking distances, starting position offset X and starting position offset Y can be changed according to the legend on the left. The compensation for one car with two parts is the compensation in the vertical direction. If it is found that every time the intelligent manipulator goes to the car to pick up parts, the position deviation is large, change this number. The six numbers of stacking positions respectively represent the number of stacked stacks A and B, and Z represents the number of stacked layers.
If the stacking position needs human intervention, you can change the number and click OK. The OK button turns green to indicate that the change is successful. When changing the palletizing settings, it must be ensured that the settings are completed before the new palletizing starts, otherwise, machine collision or paper tray damage may occur.
Exception handling
Emergency stop
When the equipment is powered on for the first time or just released from an emergency stop, the intelligent manipulator needs to release the emergency stop, confirm that the emergency stop button has been turned on, and press the red alarm reset button of the tray picking trolley cabinet. If the intelligent manipulator is in automatic mode, click the "Emergency Stop Reset" button on the system status page on the screen. When the "Emergency Stop Reset" changes from red to gray, the alarm has been released. If the intelligent manipulator is in manual mode, just press the white button light on the intelligent mechanical flashlight cabinet.
Scan barcode was unsuccessful
When the intelligent manipulator moves up and down the scanning position with the workpiece, that is, the paper, many times, it means that the scanning code is unsuccessful, so it is necessary to slow down the running speed of the intelligent manipulator. If it still has no effect, you need to click the scanning code page, check the number grabbed and scanned by the intelligent manipulator, pause the intelligent manipulator, record the barcode information that has not been scanned, and press and hold "Scan Code Skip" in the system status page until the intelligent manipulator goes to the palletizing station, and then add the just missing barcode information in MES system.
Conclusion
Today, with the rapid development of the intelligence industry, the intelligent manipulator has been widely used in the industrial manufacturing industry, but it is rarely used in the paper industry. We should vigorously promote the application of intelligent manipulators in the process of palletizing and packaging finished products, and contribute to the development of the paper industry.